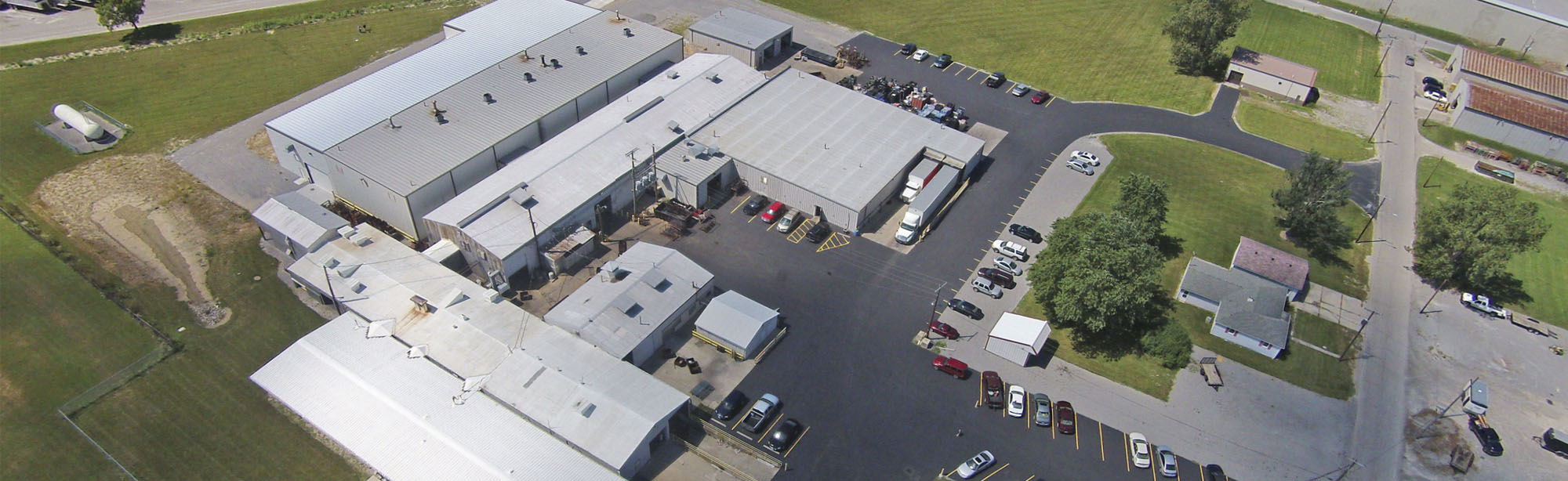
Environmentally Friendly Processes
E-coating and powder coating are eco-friendly. Let the coating experts at H.E. Orr Company help you meet the tough environmental standards of today.
OEMs put coating suppliers through their paces. They demand excellent corrosion protection with faster turnarounds and lower costs—all while keeping quality high. If this isn’t enough to challenge even the best coaters, governmental environmental standards are becoming more stringent and eco-friendly processes with a minimum of waste have become requirements.
Regardless of what is driving the decision to go green, responsible corporations know that “green is good” and take steps to install environmentally friendly processes when possible and practical. E-coating and powder coating are two of the most eco-friendly choices you can make for metal finishing.
E-coating: Excellent Corrosion Protection and Eco-Friendly
Unlike typical paint products and other liquid coatings, e-coating uses no solvents. There are virtually no harmful VOC (Volatile Organic Compound) out-gassing into the environment from an electro-coating plant. This not only makes the work environment healthier, it also minimizes the impact on the environment to help OEMs add to their list of environmentally friendly processes.
Traditional liquid and spray painting causes considerable overspray that is difficult, if not impossible, to collect and recycle. In e-coating, paint resins are suspended in a chemical bath that is mostly water. There is no overspray and almost no waste. Even as the parts are rinsed, the excess resins are reclaimed and recycled into the electro-coat bath—a closed system.
Part of being green is making products last longer. E-coating delivers better corrosion protection than conventional paint because its charged-particle, full-immersion process coats the surface of parts on a molecular level that is far more thorough than spraying.
E-coating is exceptional for complex products. It conforms to multifaceted parts and maintains designed specifications of coating thickness without runs or drips. This is especially valuable for coating the inside surfaces of parts, deep recesses, weld marks and fasteners. More parts within spec translate to less waste as well.
Powder Coating: A Hard, Durable Finish that is Easy on the Environment
As with e-coating, powder coating is also an eco-friendly choice for corrosion protection. Powder coating is applied as a free-flowing, dry powder. The main difference between a conventional liquid paint and a powder coating is the powder coating does not require a solvent to keep the binder and filler parts in a liquid suspension form. The coating is applied electrostatically and is then cured under heat to allow it to flow and form a “skin” over the part.
Powder coating is free of VOC out-gassing making it much easier on the environment than liquid paints. The powder overspray can be collected and reused. Plus disposal of unusable powder is very simple.
Powder coating is considerably more durable than liquid paints providing longer corrosion protection to extend the useful life of coated parts. Powder coated surfaces are also much more resistant to chipping, scratching, and damage in general because the finish is thicker and oven cured. It is also more resistant to natural fade and wear. It is a uniform coating that has virtually no inconsistency along a part’s surface or from one part to the next. Powder coating leaves a smooth finish with no runs, drips, or sags.
The bottom line is both powder coating and e-coating are environmentally friendly processes that deliver uniform coating which is beautiful in appearance and superior in durability. Talk to your representative at H.E. Orr Company to discover how these processes can help your company meet the tough environmental standards of today’s original equipment manufacturers.